UV ink is widely used in printing, packaging, and industrial applications due to its fast curing and durability. However, ensuring its safety requires careful evaluation of composition, certifications, and usage scenarios. Below is a step-by-step guide to selecting safe UV ink products.
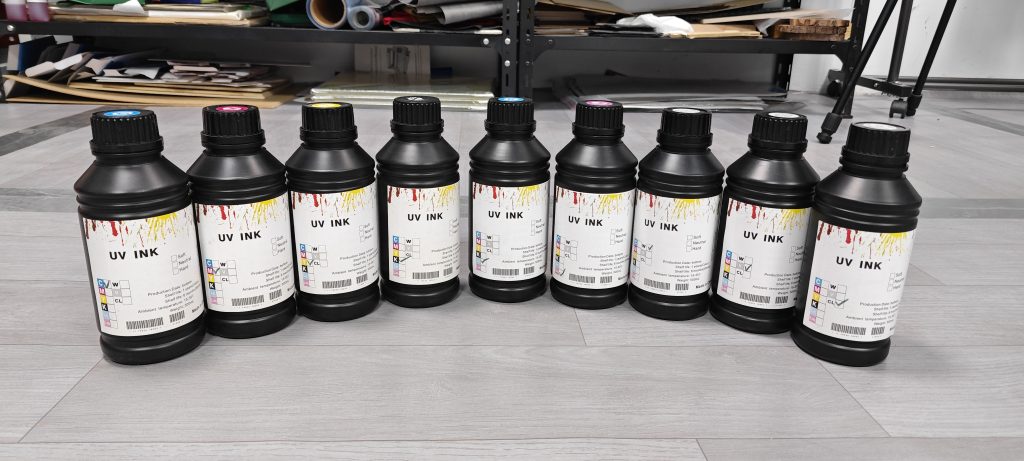
1. Verify Compliance with Safety Standards
Always prioritize UV inks that meet international or regional regulatory standards, which ensure the product’s safety for specific applications:
- Food Contact: For packaging or materials that touch food, choose inks compliant with FDA (U.S.) or GB 4806.14-2023 (China) standards. These regulate heavy metals (e.g., lead ≤10 mg/kg, arsenic ≤5 mg/kg) and require non-detectable harmful residues like aromatic amines 3.
- General Use: Look for compliance with REACH (EU) or CPSIA (U.S.), which restrict hazardous substances such as phthalates and volatile organic compounds (VOCs) 5.
- Environmental Safety: Opt for inks with low VOC content (<1%) to minimize air pollution and workplace hazards 4.
2. Assess the Ink’s Composition
Review the Safety Data Sheet (SDS) or technical specifications to identify key components:
- Avoid Harmful Photoinitiators: Some photoinitiators (e.g., benzophenone) may release toxic byproducts. Choose alternatives like phenylglyoxylates, which are safer post-curing 5.
- Check Pigments: Ensure heavy metals (e.g., cadmium, chromium VI) are absent or within regulated limits. Titanium dioxide (TiO₂) is a safer pigment option 3.
- Monomers/Oligomers: Acrylates are common but can irritate skin. Select formulations with reduced bioaccumulative potential 2.
3. Evaluate Curing Efficiency
Incomplete curing leaves residual chemicals that pose health risks. Ensure:
- Proper UV Light Exposure: Use calibrated UV-LED lamps (e.g., 365–405 nm wavelengths) for optimal curing. Mercury lamps are effective but less energy-efficient 6.
- Testing Post-Curing Safety: Conduct migration tests (per GB 31604.1) for food-contact inks to confirm no harmful substances leach into products 3.
4. Consider Application-Specific Needs
- Flexible Substrates: For plastics or textiles, choose low-viscosity UV inks that adhere well without cracking.
- Medical Devices: Use biocompatible inks certified for indirect skin contact (e.g., ISO 10993).
- Outdoor Use: Prioritize UV inks with UV-resistant additives to prevent degradation 4.
5. Prioritize Manufacturer Transparency and Support
- Technical Documentation: Reputable suppliers provide detailed SDS, curing guidelines, and compliance certificates 2.
- Custom Solutions: Some manufacturers offer tailored formulations for niche applications (e.g., heat-resistant inks for electronics) 6.
6. Implement Safe Handling Practices
Even certified UV inks require precautions:
- Personal Protective Equipment (PPE): Use nitrile gloves, goggles, and masks to avoid skin/eye contact with uncured ink 5.
- Ventilation: Install local exhaust systems to reduce inhalation of aerosols or fumes 4.
- Waste Management: Dispose of uncured ink and contaminated tools as hazardous waste to prevent environmental contamination 7.
7. Monitor Industry Trends and Innovations
Emerging technologies enhance UV ink safety:
- Bio-Based Monomers: Derived from renewable resources, these reduce dependency on petrochemicals 4.
- Water-Based UV Inks: Lower VOC emissions and easier cleanup compared to solvent-based alternatives 5.
Conclusion
Choosing safe UV ink involves balancing regulatory compliance, composition analysis, and application requirements. Always prioritize certified products, validate curing processes, and adopt protective measures. By staying informed about advancements in eco-friendly formulations, businesses can align with global sustainability goals while ensuring user safety.